Welding of stainless steels
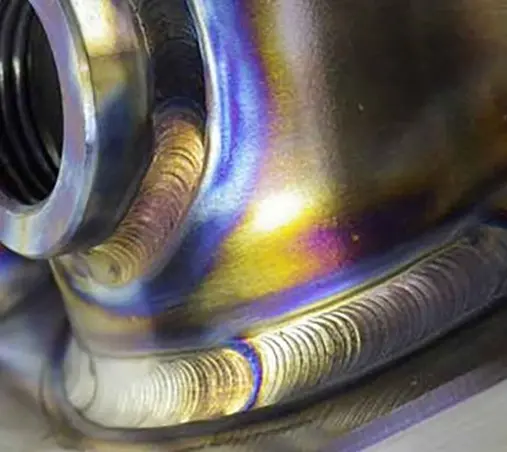
Quality welding of all stainless steels
Author: Nacho Chinchilla, Ingenieria de Integración y Soldadura, Consultoría y Formación
All types of stainless steels, as a general rule, are weldable, although logically some technical and operative precautions must be put into practice together with the disposition of the quality criteria, and above all the constructive purpose for which it was designed.
On the basis of the above, not only the welding process, but also the acceptance and rejection criteria in terms of quality and the additional safeguards to be taken into account in the welding process will be determined.
We must be clear that all stainless steels, regardless of their chemical-mechanical composition, are highly resistant to corrosion and to the multiple service conditions for which they have been designed; but on the other hand, they are highly oxidisable when the melting point is reached and the product is exposed to the surrounding atmospheric conditions, i.e. the air we breathe.
This will lead to a carburation by chromium depletion, which will facilitate the appearance of a zone of unweldable “charcoal”, and therefore oxidation (see photos).
Image type of TIG welding in which if the root is not protected inside, we have, “penetration “Contaminated
Additionally, in some cases some types of stainless steel may be affected by the thermal effect of welding, and undergo transformations and modifications in terms of their physical-mechanical capacities, which in some cases will affect the service conditions for which they were designed, which is why it is sometimes essential to know the relationship between Cr and Ni, equivalent to the Ferrite Nº “FN” content.
But above all from an operational point of view, processes with the lowest possible thermal input should be used with the highest possible welding travel speed, which reduces the problems described.
It is therefore extremely important to know and control several factors when it comes to welding stainless steel.
- Type of base material combined with type of filler material
- Type of electric arc
- Welding thermal input
- Pre or post welding preparations
- Exhaustive control of the protection of the base material, especially if there is penetration.
- Part preparation, use of ceramic backing or support surfaces and/or heat dissipation, as well as the use of support gas, support or drag gas, by means of “boxes, pipe deflectors”, etc…
Automation and Robotization significantly reduce these problems through process stability.
For more information on this product, please contact us.
Share this post: